Proven Methods used in a new way
Our ADORBOND alloy powders - high quality for digital processing.
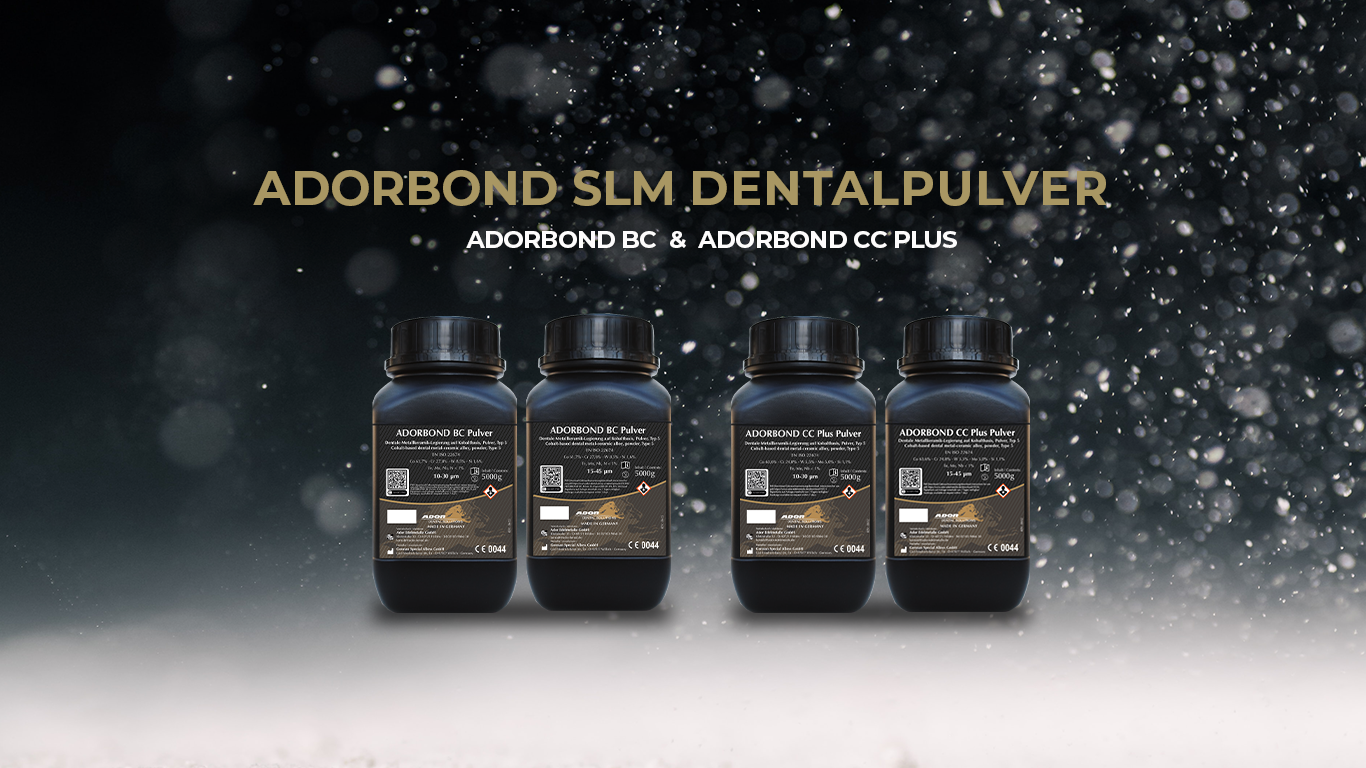
As one of the few certified european Manufacturers We supply high quality precious metal free Dental alloys from our own production. This also includes dental powders of the series ADORBOND, which are free of nickel and beryllium and also comply with the EN ISO 22674 Type 5 standard. This means that you can obtain from us not only burn-on alloys, but also pattern casting alloys.
Our ADORBOND powder in the grain size 10-30µm offer you with a one of a kind advantagethat they are not only meant for burning on suitable, but also for Modeling cast alloys are applicable. In this way you save time for that would have went into cleaning the machine and material changes Material changes is also not necessary.
Advantages of ADORBOND® BC powder - NEW!
- Biocompatibility
- Free from nickel, beryllium, cadmium and lead
- Particularly good for applications with thin cross-sections that are exposed to very high forces
- Can be used as a burn-on and pattern casting alloy
- CE- Certified
- Depending on the ceramic, no cooling phase is necessary
- Available in grain size 10-30µm and 15-45µm
Benefits of the ADORBOND® CC plus powder
- Biocompatibility
- Free from nickel, beryllium, cadmium and lead
- Particularly good for applications where the fixture parts require a combination of high stiffness and yield strength
- Can be used as a burn-on alloy
- CE- Certified
- Depending on the ceramic, no cooling phase is necessary
- Available in grain size 10-30µm and 15-45µm
The SLM Procedure
Selective Laser Melting
Selective laser melting, or SLM for short, is probably the most modern method of manufacturing dental restorations. In selective laser melting, the dental alloy to be processed is built up in thin layers in powder form. The dental alloy in powder form is completely remelted locally by the laser beam and forms a solid material layer after solidification. The 3D design data for the laser is supplied by the appropriate CAD software.
When the powder has cooled and solidified on the component contours, the base plate is lowered by the amount of one layer thickness and the powdered dental alloy is applied again. This cycle repeats accordingly until all layers have remelted. One argument in favor of this additive manufacturing is the high specific density of the finished components. No additional tools or molds are needed either, and only as much material is consumed as is required for production. Excess material can be reprocessed. With this process, you can flexibly implement shapes of any complexity, and you save resources and the environment: You can subsequently process the excess powder without any loss of quality, and you can simply recycle unused metal powder.
Powder Metallurgy
Powder metallurgy is a derivative of metallurgy, which is essentially concerned with the production of metal powders and their further processing. The manufacturing process is characterized by the mechanical compaction of metal powders in molding tools or pressing and sintering of the blank at high temperatures or hot rolling into an ingot. The result is solid, fine-grained semi-finished or finished parts.
Do you have further questions?
Make an appointment with an ADOR representative right now and learn more about how digital dentistry can make your work processes more efficient.
Fair prices
Excellent conditions and continuously attractive promotions
High quality
With us you will find only certified quality products
Simple & fast
Excellent conditions and continuously attractive promotions
Top advice
Competent and personal advice with many practical ideas